- Communicating product requirements with your QC staff and suppliers
- Communicating your specific requirements for packaging
- Defining onsite tests and inline tests with your supplier and factory
- Defining your classification terminology with your supplier
- Establishing a perfect sample
- Conducting DUPRO quality control
- Conducting after production quality control
Communicating your product requirements with your QC staff and suppliers can help prevent quality defects
Communicating your product specification with your supplier is essential to safe guarding against product defects.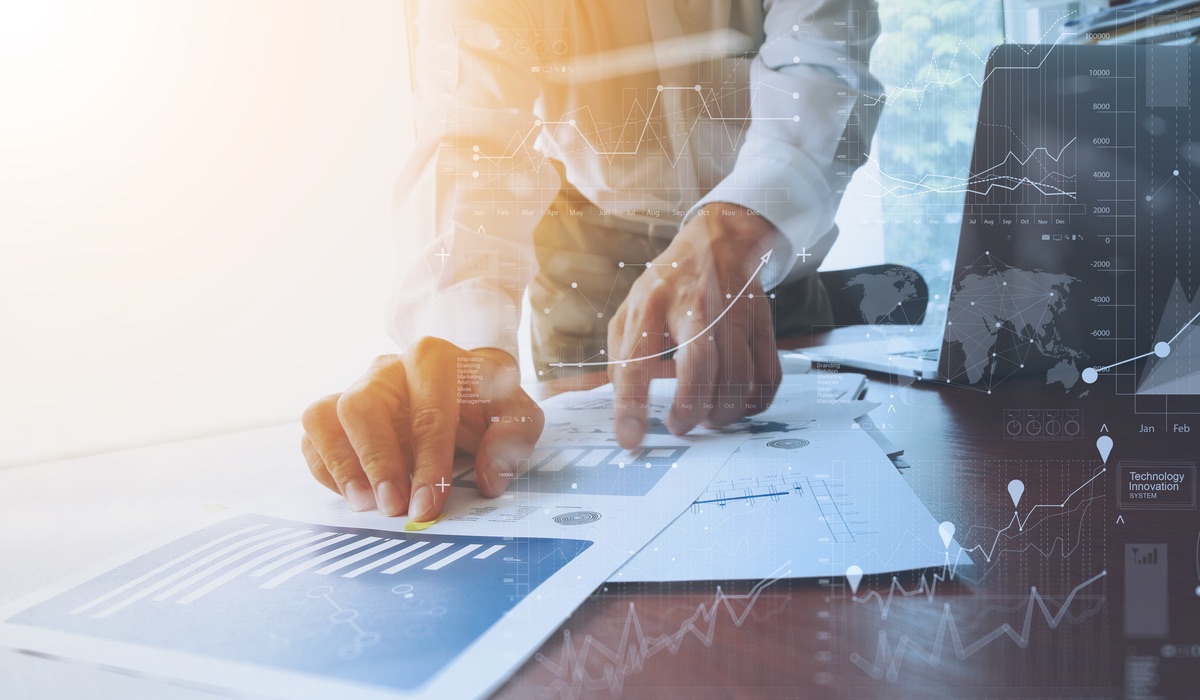
Communicate your packaging requirements to Prevent product defects
Your product needs to meet packaging requirements when shipped. This will often mean that all the necessary documentation will be present and/or visible on the package during the import and export customs process. You need to specify the packaging requirements and what exactly needs to be present on the outside of the box. This will safeguard against possible damage during shipment, ensuring their safe arrival.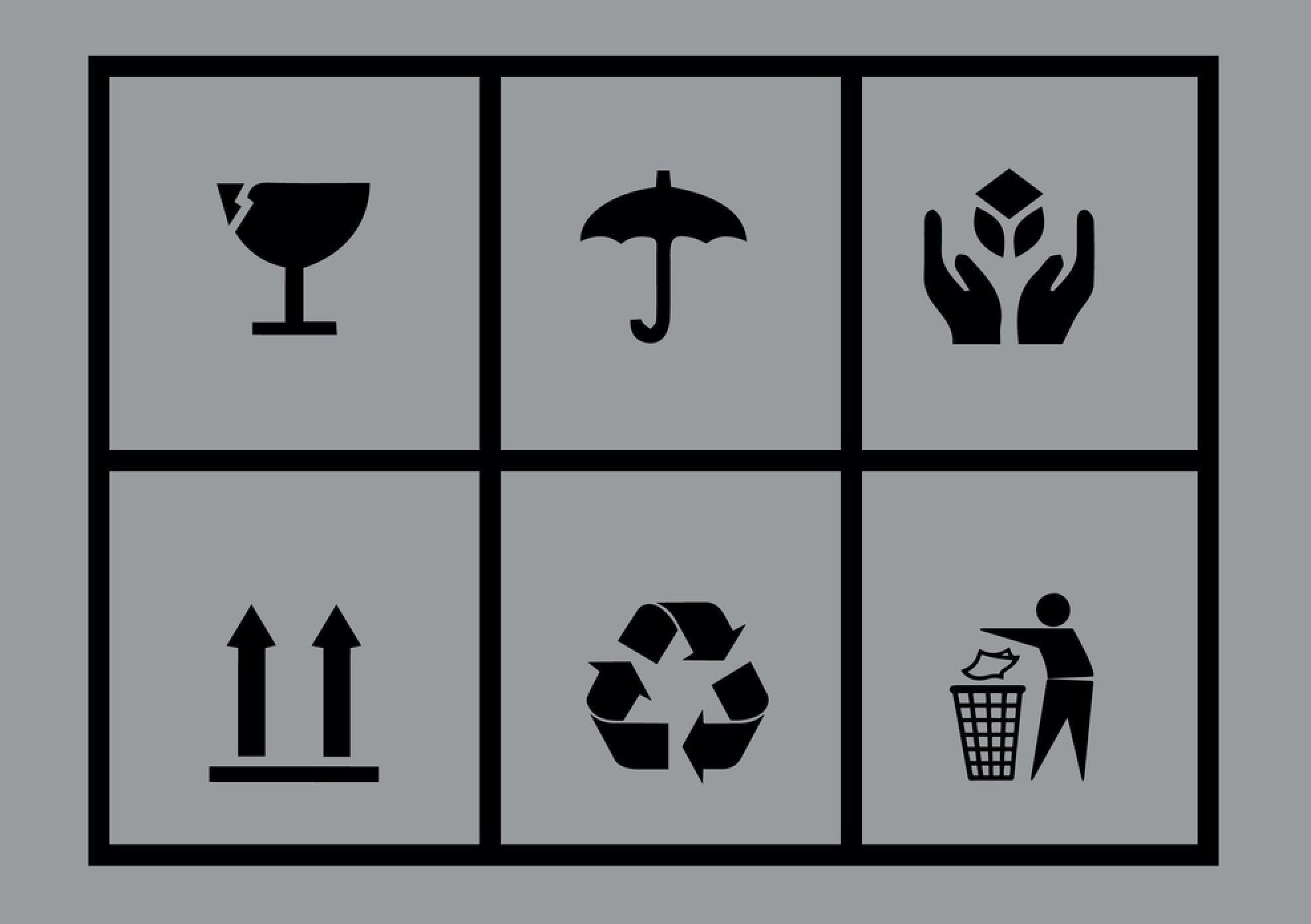
What onsite tests and checks will you be doing?
Your quality control team, whether an in-house or outsourced team, have to be informed about the types of quality tests that need to be conducted on site. Once you confirm what tests are needed, your inspection team will need to know what testing equipment is needed per product. An electrical juicer for example will be tested differently to what tests will be needed for other product categories. If you choose to use an experienced third party quality provider you will be able to leverage their technical expertise, for example, the exact type of load testing that may be needed for a couch that is destined for the European market. An experienced third party provider will also have labs with controlled environments and all the right equipment to test your product, along with the constant monitoring of any updates in regulation that you may need to be aware of.Have you agreed upon the defect classification terminology?
Many importers choose to use the following classification terminology when dealing with their suppliers:A critical defect – This is defined when the product may cause possible injury or harm to the end user. This product’s safety is compromised.
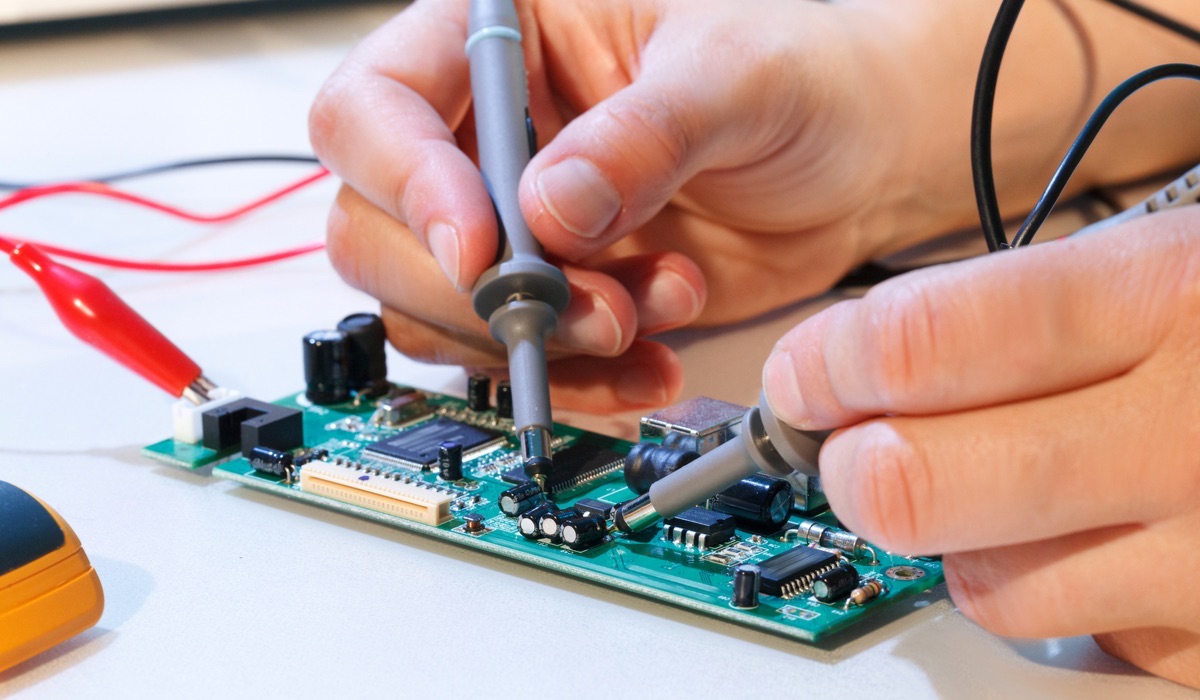
Where the product in question can cause injury to the end user, this results in product recalls and is hugely damaging to your brand.
A major defect – This is defined when its condition will affect the sale of the product in the marketplace, likely resulting in the end user returning it with dissatisfaction.
A coffee maker that does not heat the water adequately to make a decent, drinkable cup of coffee is classified as a major defect.
This product has caused dissatisfaction amongst its end users and they then return it to the store, likely reviewing the product online, which will have an impact on the future sales of that item.
A minor defect – This is defined when its defect is small, and will not affect its saleability in the marketplace and does not pose any harm or injury on the end user.
Take a wooden coffee table for example. Your quality control teams takes the product through its tests and they come across a scratch underneath the table.This is a scratch that your end user will not see in normal use of the product or may never even see it for that matter. This is what we would classify as a minor defect where this product will still go to market as it will not cause any damage or harm to the end user.
But that’s not all…
What about a sample? I have left obtaining a sample for the end…as some importers don’t require a sample before production. While this is not a necessity, by adding this into your production procedure it can help you significantly reduce product defects that come from your selected supplier and factory. Once you have established the appropriate product requirements, you can then request a sample from your supplier. Once you receive your sample you need to analyze it and ensure that it meets all of your requirements, and then send it back to your supplier with either a confirmation to go ahead with your production, or with a list of further specifications that they need to meet. Well, what happens if it doesn’t meet your requirements? Samples will not always meet your specified product requirements. Often times you can catch this just by holding or looking at the product. But, more often than not a substandard product of will reach the end consumer opening your brand up to severe damage and risk.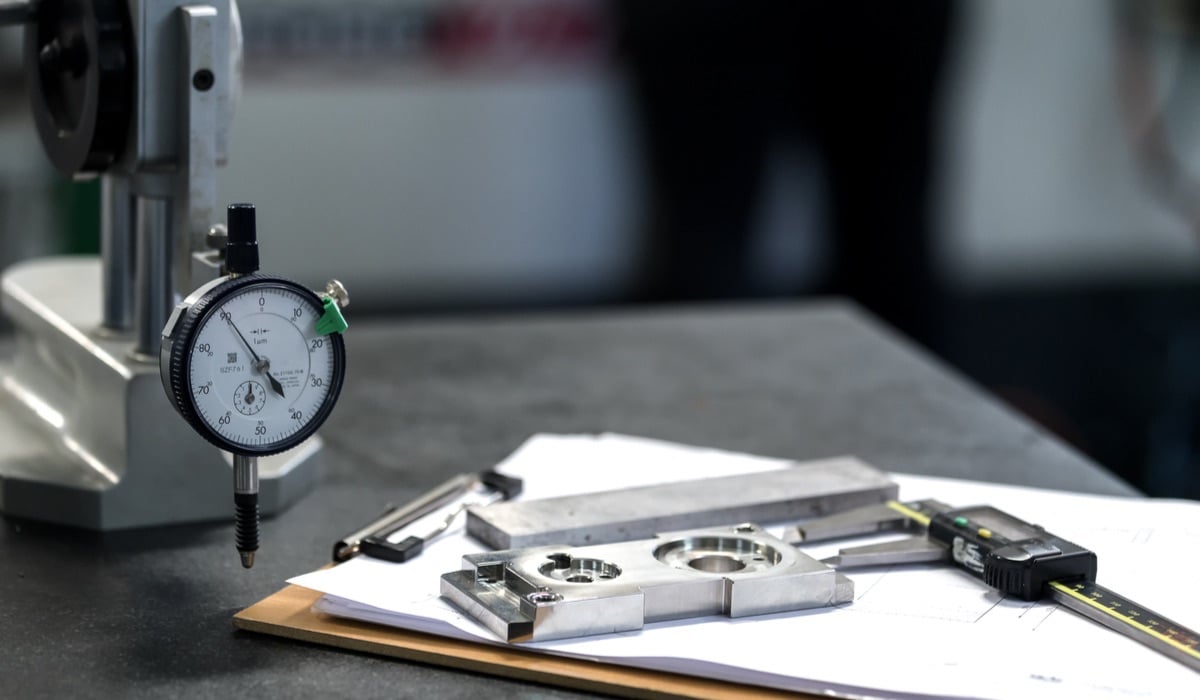
How to manage quality during your mass production process?
During the production process, there is often a variation in the quality of the products. This is why you should be employing a factory quality control team to minimize this scope of variation. This team does this through inline production checks that will identify any defects that can be amended on the production line. During your supplier selection phase you would have done an analysis on the success rate of your factory. This will help you determine whether or not you should outsource your inline inspections to a qualified third party quality provider. Their production line expertise will help raise the level of the overall quality system of the factory, therefore minimizing the number of product defects coming out of the factory.You can also secure the quality of your production through final inspection controls
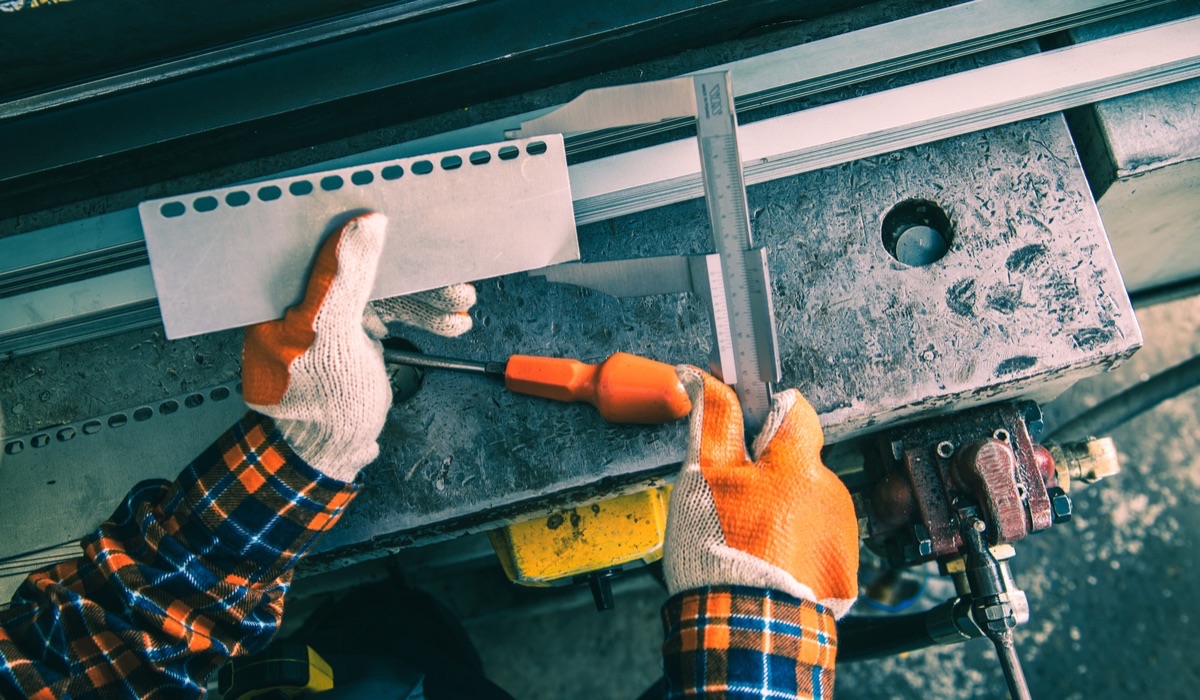
Key Takeaways
Product defects are not ideal, suppliers hate them as much, if not more than you do. By following the guide laid out above, you will be setting a solid foundation on which to begin minimizing the amount of product defects that you experience. So let’s round this all up:- Communicate your product requirements
- Communicate your packaging requirements
- Defining onsite tests and inline tests
- Defining your classification terminology
- Establish a perfect sample
- During production quality control process needs to be defined
- After production quality control process needs to be defined